Contractors tasked with maintaining roadways face a recurring challenge: time is money, and both often run in short supply. The pressure to deliver quick and quality road repairs is ever-present.
To meet these demands, contractors must adopt innovative solutions that allow them to get the job done right while saving time, money, and resources. Outdated or inefficient equipment simply won’t suffice when dealing with the intricacies of modern infrastructure projects.
The hotbox is an underutilized tool that’s transforming road repair. Traditionally used to fill potholes, contractors and utility companies now use these versatile machines for repairs around utility cuts.
Read on to learn how a hotbox can cut costs, improve efficiency, and save time.
The Problems with Traditional Pothole Repair Methods
Contractors often use quick fixes like gravel, metal plates, or cold patch asphalt for road repair of utility cuts. However, each method comes with its own set of particular challenges:
Gravel Filling: Using loose gravel to fill potholes is a quick and cost-effective method. However, it’s not very durable. Traffic can easily displace the gravel, causing more road damage and requiring repeated repairs. Loose gravel can also damage vehicles and be a hazard for motorcyclists.
Metal Plates: Using metal plates offers a temporary solution for covering potholes and allows vehicles to pass over safely. However, they often lead to a noisy and bumpy driving experience.
If not properly secured, they pose a risk of shifting and can become a hazard. Moreover, the need for ongoing inspections makes metal plates a less-than-ideal choice for long-term road integrity.
Cold patch asphalt: Involves using a premixed material that hardens over time. It’s more stable than gravel but still a short-term solution. It may not bond well with the surrounding pavement, leading to weak spots. Repairs with cold patch asphalt often deteriorate faster than those with hot mix asphalt.
Many contractors must complete a solid and permanent repair to receive full payment. This urgency requires them to quickly find solutions that last and avoid temporary fixes that often lead to more work and expense.
The Advantages of the Utility Cut Method
Utility cut asphalt patching goes beyond typical pothole repairs by providing a long-lasting repair. The key advantages of this method include:
Speed of Execution: Utility cut asphalt repair allows for the prompt completion of the repair. This quick turnaround is crucial for reducing traffic congestion and getting businesses back to normal as soon as possible.
Year-Round Patching: Using hot mix asphalt enables contractors to carry out permanent patches throughout the year, regardless of the season. This flexibility ensures that road maintenance and safety are not compromised by cold weather or other seasonal challenges.
High-Quality Repair: Hot mix asphalt creates a more durable and seamless repair, increasing the longevity of the road surface compared to temporary fixes. A longer-lasting repair means fewer resources and less time spent on future roadwork, offering better value over time.
An important aspect often overlooked is the financial impact on contractors. In many cases, contractors are not fully paid until the permanent patch is applied. This can affect their cash flow and project scheduling.
Using Falcon’s efficient trailer and truck-mounted hotboxes can speed up the process of making permanent repairs. This ensures quicker road openings and faster full payment for contractors, improving their financial stability and project turnover.
Falcon’s Equipment: A Game-Changer for Efficiency
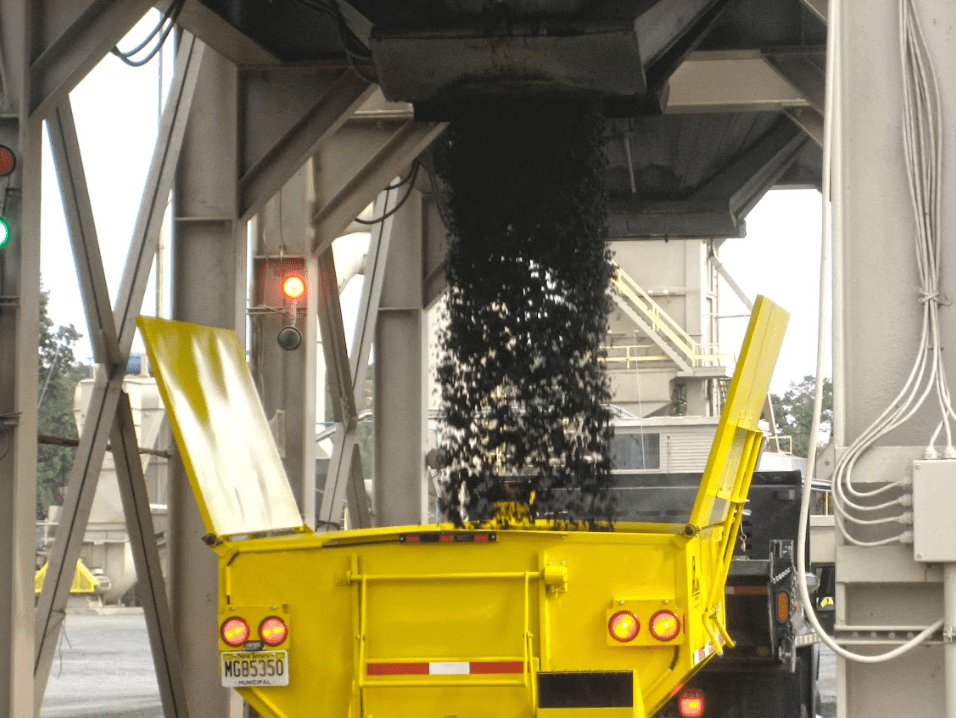
Falcon’s equipment extends beyond the general scope of pothole repairs. Many water departments and contractors utilize our hot boxes for utility cut repairs. The unique design of these hot boxes saves time and money.
Additionally, we offer Trailer Mounted Asphalt hot boxes and Patch Trucks, each specifically designed for the demands of utility cut asphalt patching. Contractors can easily bring our hotbox to the work site for immediate use. Our Patch Trucks are great for teams doing a lot of asphalt repairs in one day. This is especially helpful when there are many utility cuts close together.
Falcon’s equipment offers specific advantages that directly address contractors’ needs. The ability to quickly complete jobs is crucial. Contractors can apply hot mix asphalt year-round, ensuring permanent, high-quality repairs regardless of the season.
This efficiency is a major advantage over traditional methods that often lead to delays and extended city repair processes. These features of Falcon’s equipment not only streamline operations but also significantly reduce the frustration associated with long repair timelines
Hot Boxes and the Utility Cut Repair Process
With Falcon’s Trailer Mounted Asphalt hot boxes, contractors can access hot mix asphalt at the job site. These hot boxes can be easily towed, which means an uninterrupted workflow and an immediate start to repair processes once underground work is done.
Patch Trucks for Bulk Repairs
Falcon’s Patch Trucks are invaluable for crews responsible for daily permanent asphalt repairs. Having a patch truck allows for efficient, quick repairs on group utility cuts and leads to better project turnover time.
Streamlining Operations and Profitability
The combination of Falcon Asphalt equipment’s functionality reduces downtime and operation costs and significantly boosts contractors’ profitability. Falcon’s equipment delivers top-quality repairs. The fixes they enable are durable and budget-friendly. This matches the urgent road repair needs crews to handle today.
Embrace the Best with Falcon Asphalt
Utilizing an advanced hotbox solution saves time and money compared to short-term gravel, cold mix, or metal plate approaches. Falcon’s innovative equipment enables contractors to conduct swift, high-quality, year-round repairs that reopen roads faster.
Click below to learn how to choose a pothole truck that aligns with your operations.
Recent Comments