As pavement ages, it tends to distress in certain areas due to traffic and environmental factors. If these minor potholes aren’t remedied quickly, however, they grow into even bigger ones.
Ask any mayor or city council member—potholes are one of the most frequent complaints they hear. As election day draws near, the pothole situation is fresh on voters’ minds as they head to the voting booths.
Community members like seeing public works departments who are out fixing roads with purpose-built equipment because they can see the immediate results of their tax dollars being put to good use.
When it comes to repairing potholes, several challenges often present themselves. Read on to learn more about the biggest problems that can arise when patching potholes—and the correct way to solve them.
Pothole Repair Issues
Asphalt pothole repair is a relatively simple process. The exact method chosen to repair depends on the size of the crack or hole. However, the most popular repair methods include “crack sealing” or filling the pothole with cold or hot mix asphalt.
However, several issues often manifest themselves when patching or repairing a pothole including the following:
Using Cooled/Cooling Material
When workers use material (either cold mix or hot mix) that is not at an optimal temperature, it’s inefficient and causes waste. Repairs made with this material are less effective and within days, weeks, or months, the potholes reappear seemingly out of nowhere.
Even if the material was at a usable temperature at the beginning of the day, it cools fast and becomes increasingly difficult to work with as the clock ticks. Workers are often stuck in the “it’s always been done this way” mentality of putting hot asphalt in the bed of their trucks. By the time they get to the pothole, it has already cooled and is harder to work with.
In the end, supervisors usually chalk up the extra asphalt expense as the cost of doing business, and crews repeatedly repatch the same potholes.
Ergonomic Problems
Shoveling material from raised truck beds requires the workers to lift the shovel above their shoulders, scoop up asphalt material at awkward angles, and then bring it back down to the ground.
This process causes tremendous stress on the worker’s backs and upper bodies, which can lead to disability or workers’ compensation claims. It’s also highly inefficient—the guy with the shovel full of heavy asphalt tends to work much slower.
Check out this demonstration to see the huge shoveling height difference between a traditional truck and a Falcon hotbox:
Poor Quality Asphalt
Low-quality asphalt used for filling potholes won’t hold up over time. Patches break down quickly as cheaper varieties fail to adequately bond with the road surface. Water and traffic break the material away from the road when asphalt doesn’t stick well. The pothole eventually resurfaces within a few weeks.
Crews must use high-quality material formulated to withstand wear from tires and the impacts of weather when patching potholes in asphalt. Only high-bond varieties will deliver long-term pothole fixes without constant re-patching.
Here’s how you can assess the quality of your asphalt:
Color—High-quality asphalt usually has a uniform black color. It might be a sign of poor quality if you notice shades of brown or gray.
Texture—The surface should be smooth and consistent. Rough or uneven texture can point to quality issues.
Adhesion—Good asphalt sticks well to the aggregate, making a firm, unified surface. Poor adhesion often results in loose gravel and premature wear.
Smell—Fresh, high-quality asphalt has a strong petroleum smell. A stale or off odor can indicate that the material has oxidized, affecting its quality.
Hot Boxes and Patch Trucks
Hot boxes and patch trucks can solve many pothole repair problems. This purpose-built equipment allows workers to transport asphalt to the job site and make repairs efficiently.
Hot Box
Hot boxes are insulated and heated containers designed to keep asphalt at optimal temperatures for 72 hours. They come in trailer and truck-mounted versions, each ideal for specific use cases.
For example, trailer-mounted versions are ideal for navigating city traffic and narrow streets, while truck-mounted hot boxes integrate directly into truck beds, allowing convenient transportation to job sites.
Patch Truck
These customized trucks are specifically engineered for asphalt and pothole repairs. They come with built-in hot boxes that maintain optimal temperatures to preserve material quality. Ergonomic designs prioritize crew comfort, safety, and efficiency when performing repairs.
Customized engineering and interchangeable attachments adapt each truck for varied jobs. This optimizes productivity and enables crews to deliver durable, high-quality road maintenance.
Benefits of Using a Falcon Hot Box
A Falcon hot box is the ideal solution to all the above problems. When using a hot box to keep the material at the correct temperature, you will increase the efficiency of your operations while saving money on material and labor.
The repairs will last longer. This means fewer trips back and forth to the same pothole, and fewer trips mean less material used and more money saved. With a Falcon hot box, you can also hold material overnight for up to 72 hours and save unused material versus wasting it.
Your workers (and their shoulders, arms, and backs) will also thank you since a Falcon hot box allows for the ergonomic loading and unloading of asphalt material. This directly translates to increased efficiency, fewer workers’ comp claims, and better employee retention.
Exclusive VIP Technology
Falcon hot boxes stand out with their innovative and exclusive Voltage Indicator and Protector (VIP) system. This proprietary technology prevents burner activation unless voltage levels are optimal for safe operation.
The VIP feature illuminates a green indicator light, signaling the operator when battery voltage can support burners. By regulating operation based on power levels, the intelligent VIP technology maximizes durability and extends the lifespan of Falcon hot boxes.
Other benefits of a Falcon hot box include:
- Fewer trips to the asphalt plant
- Keeps asphalt at optimal temperatures for up to three days
- Ability to recycle asphalt chunks and millings with an optional 2nd burner
- Prevent asphalt from cooling and becoming unusable
- Enable crews to work efficiently with decreased downtime
- Help reduce waste from cooled, discarded asphalt
How Hot Boxes Can Save Money
Generally speaking, you can conservatively reduce the number of trips to repair the same pothole by a ratio of 3:1 to 5:1 or a 60-80% savings in material and labor.
It is also reasonable to believe you can reduce material waste by 10-20%. Falcon hot boxes also reduce operator fatigue, thereby increasing efficiency and operator safety.
Types of Hot Boxes
Falcon makes several different types of hot boxes, each with its unique benefits:
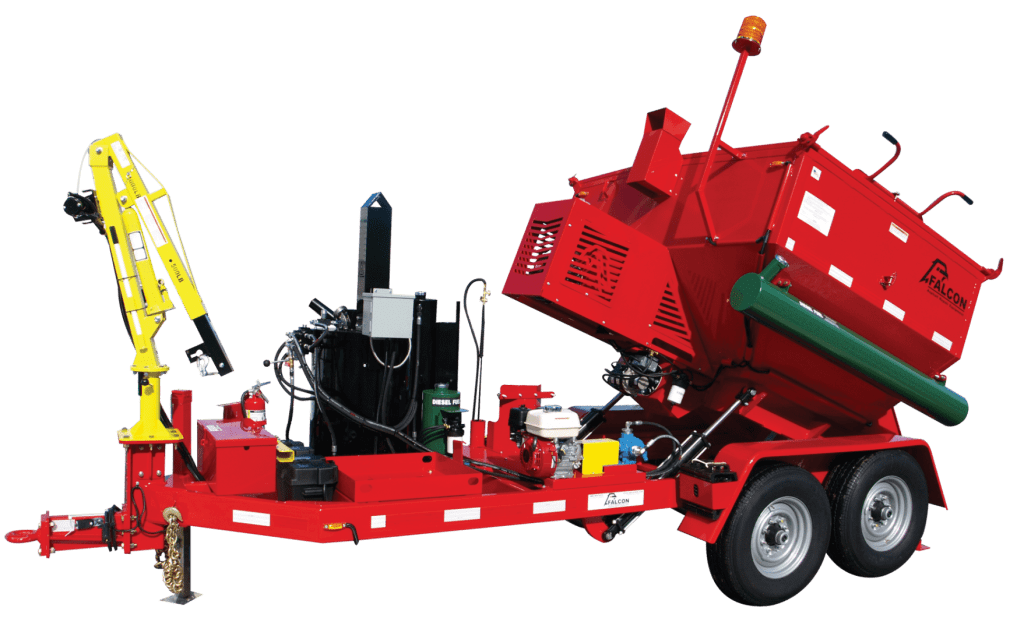
Dump Box
The Dump Box is our most popular asphalt hot box and recycler. With the push of a button, it cleanly dumps asphalt onto the ground. We construct the Falcon dump box trailers using two hydraulic cylinders that prevent twisting from uneven loads. Available in 2, 3, 4, or 6-ton capacities
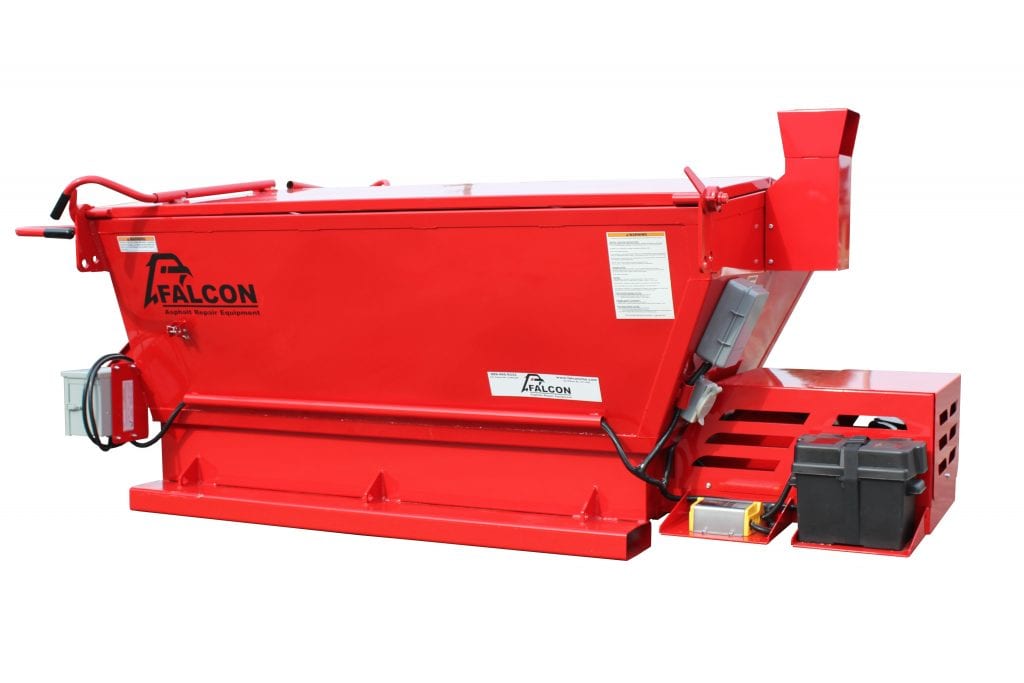
Truck-Mount/Slip-in Hot Box
You don’t have to run out and buy a trailer to keep your asphalt warm—Falcon truck-mount hot boxes slide into the bed of a standard pickup truck.
They’re available in 2, 3, 4, 5, 6, 8, or 10-ton capacity. We can also configure them with a self-dumping capability or customized sub-frame for hook-lift, roll-off, or chassis-mount systems.
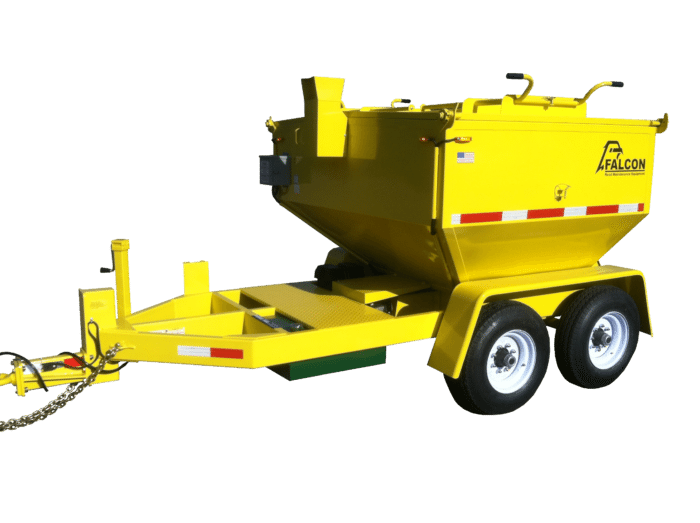
Trailer Asphalt Hot Box & Recycler
Our trailer hot box uses a stationary hopper and comes in 2, 3, or 4-ton capacities. You can have it built with either one or two burners, and it comes with a full line of customized options.
The Falcon Patch Truck
The 4-ton Falcon Patch Truck is in a class of its own. Unlike many other models on the market, it does not require a CDL license to drive. This massive advantage eliminates the high costs of hiring and retaining licensed CDL drivers.
With no conveyor or auger, the streamlined Falcon has fewer moving parts that can break down and cause lengthy repair downtimes. A simple design in combination with high-quality, durable components maximizes uptime for continual productivity.
Other benefits include:
- Flexible material delivery speed and amount
- Lower maintenance and operating costs
- Ergonomic design reduces repetitive motion injuries
- Lack of hydraulics improves fuel efficiency
- Holds material overnight for earlier start times
Solve Your Asphalt Patching Problems With a Falcon Hot Box
A Falcon hot box can save time, money, and eliminate the most common problems municipalities and contractors face when repairing asphalt potholes.
Click below to learn more about our hot boxes and patch trucks.
Recent Comments